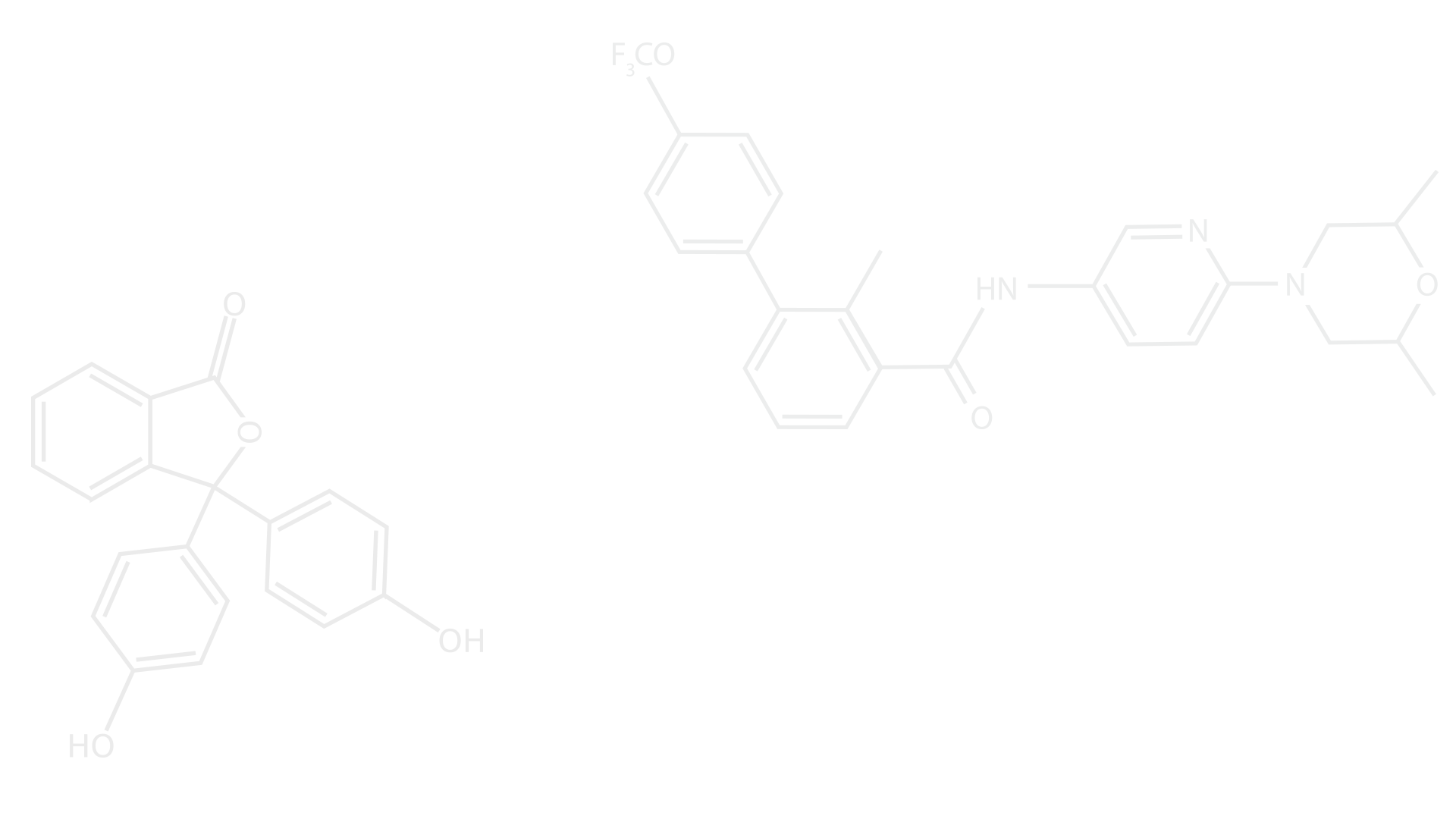
Investigating the Role of Catalysts in Pyrolyzing Low-Density Polyethylene to Produce Heptane
General Overview
Plastic is a modern necessity, given its prevalence in products we use daily. However, the massive quantity of plastic being produced annually produces two significant problems. With 300 million tons of plastic produced in 2016, it needs to be disposed somewhere, and usually it will land in a landfill or the ocean. Plastic takes hundreds of years to degrade, meaning that once it enters the environment, it will remain there for a very long time. This leaves organisms at risk of eating and suffocating on the plastic waste, and toxic additives in the plastic may leach into the environment. Plastic is also made from a non-renewable resource, namely petroleum; based on current estimates of consumption and oil remaining, an event called peak oil will occur at around 2050, when it becomes uneconomical to drill for more oil because it has essentially run out.
​
With these two problems in mind, the purpose of this research was to recover the original hydrocarbons used in the manufacture of plastic through a process called pyrolysis, where the long chains of hydrocarbon units are broken into shorter chains by heat. This process is rather inefficient, requiring temperatures between 300 and 900 degrees Celsius, so in this research, calcium hydroxide, nickel hydroxide, aluminum (III) oxide, and iron (III) oxide were tested to see if they could act as catalysts for this process with low-density polyethylene (LDPE) plastic.

An example pyrolysis reaction with part of an LDPE chain. Granulated LPDE.

In this experiment, 5 grams of granulated LDPE plastic were heated to 400 degrees Celsius for 40 minutes in the presence of 2.5 grams of each catalyst plus no catalyst as a control, and a second round of data was done at 500 degrees Celsius as well. The original intent was to obtain a liquid product to fractionally distill for heptane, a component of gasoline, but unfortunately not enough liquid could be made to collect in the desired flask. As such, the amount of mass lost to gas needed to be used. At 400 degrees Celsius, aluminum (III) oxide lost the most mass to gas and was the only catalyst at that temperature to consistently produce oily residue. At 500 degrees Celsius, nickel hydroxide lost the most mass, but due to the significant black discoloration and brittleness, this is likely due to combustion, not pyrolysis. Aluminum (III) oxide thus lost the most mass to gas from pyrolysis at 500 degrees Celsius, and it also had much more liquid residue deposited on it than the control when measuring the masses of the flasks used.
​
Given aluminum (III) oxide's high conversion rates to gas, it seems promising as a catalyst for pyrolyzing LDPE, although more research needs to be conducted that extracts an actual liquid product for identification. Conducting this experiment under a nitrogen or argon atmosphere is necessary to prevent combustion. With this and future investigations, new recycling methods can be developed that recover the original hydrocarbons so that they may be reused, reducing dependence on oil from the ground and keeping plastic out of the environment.