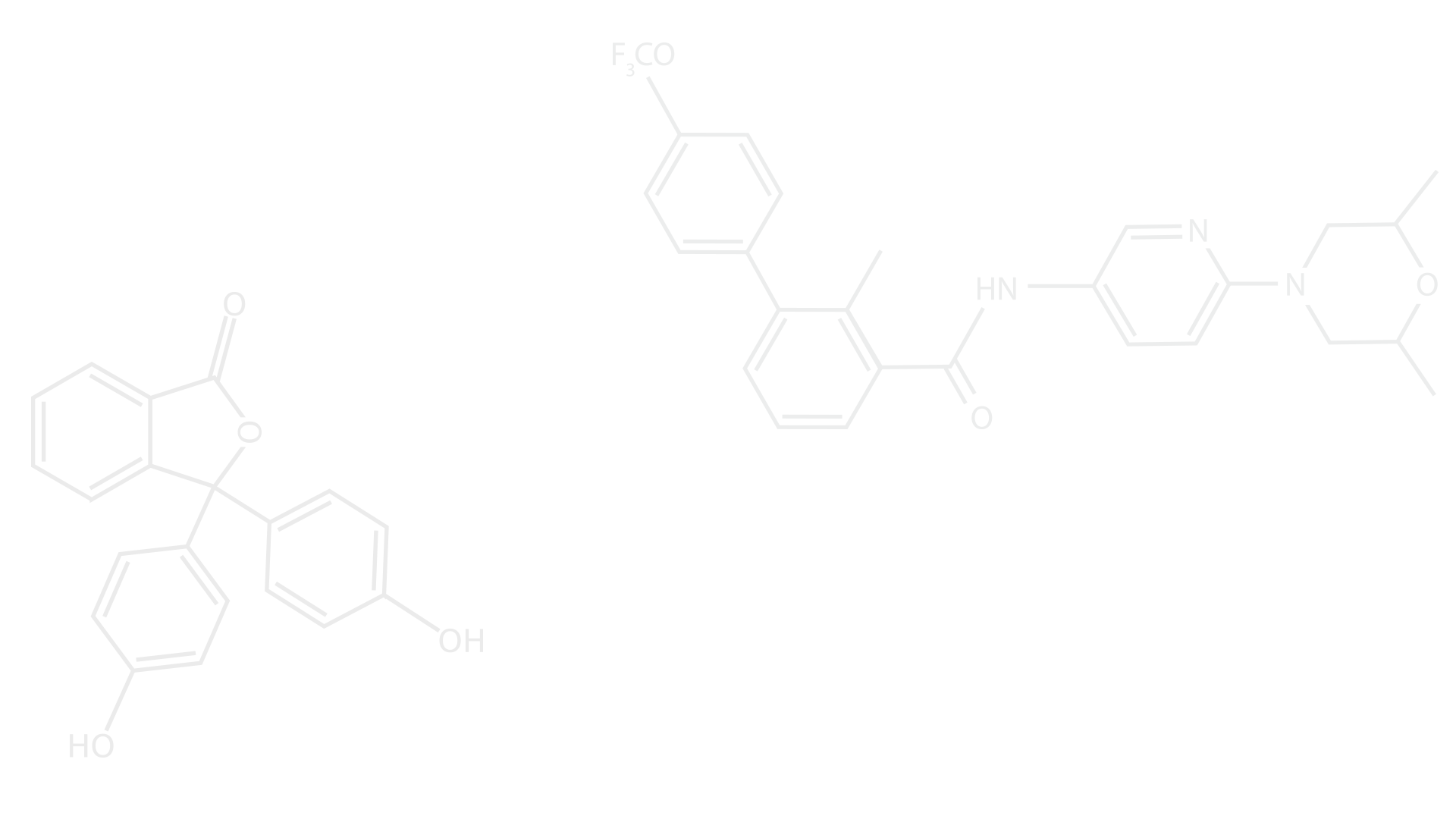
Quality Engineering at Panasonic Energy of North America
General Overview

As research pushes the boundaries of what is physically possible with electrochemistry, industry pushes the boundaries in scaling up advanced energy storage technologies. Panasonic Energy of North America (PENA) is at the forefront of this boundary, manufacturing more than 5.5 million batteries per day at its Tesla Gigafactory location near Reno, Nevada. Specifically supplying cylindrical lithium-ion cells for electric vehicles, PENA's mission is to make affordable electric vehicles a reality by manufacturing the world's safest, high-quality, and cost-effective batteries, pushing towards more sustainable energy and transport infrastructure.
​
As a summer 2022 intern, I worked in the quality engineering department, harnessing the multidisciplinary expertise of materials science and my own research experience to ensure that all manufactured cells meet strict safety and performance standards. To address the sheer scale of operations within the factory, I stepped out of my comfort zone in exploring new problem-solving paradigms and developing new technical skills, resulting in a great development of my data analytics skills.
​
Above: The Tesla Gigafactory, which Panasonic operates in part to manufacture cylindrical Li-ion cells for its customer Tesla.
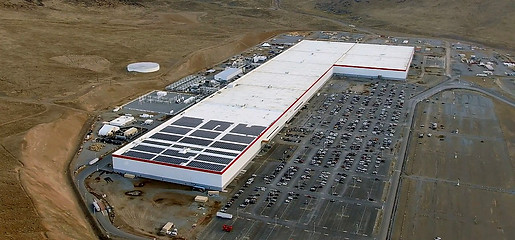
Harnessing statistical hypothesis tests and machine learning methods such as logistic regression, I developed models that found relationships between defects and predicted them before they occurred using quality inspection data. This data analysis served as both a prediction mechanism and fundamental insight into the inspection process, highlighting its shortcomings in catching defects due to poor time resolution, database flaws, erroneous measurements, and more. As a result of these insights, I led several initiatives to improve the measurement resolution of inspections, resolve technical issues that limited the scope of inspection data analytics, and expand individual cell tracking in manual inspections. I harnessed existing RFID systems within the factory, authored trainings for using superior measurement instrumentation, and coordinated with the SCADA team to execute these initiatives, ultimately yielding an estimated $110,000 in yearly savings after the brief summer internship.
​
The interns I met through this experience were absolutely delightful, and I am immensely grateful to have met such a spirited and talented set of engineers through this internship. In collaborating with the other interns in the quality engineering department, I facilitated work studies for the implementation of new standard operating procedures (SOPs), assisted interns with scripting, and organized presentations for all-hands meetings. In return, they provided an incredible source of technical expertise and industry knowledge while making time spent outside of the work energizing and rewarding.
​
Interning at PENA has provided invaluable knowledge into the battery manufacturing process, electrode design considerations, and the materials engineering that has delivered some of the most energy-dense and safe batteries commercially available.